Kitchens are a high risk area. They are the subject of a number of Australian Standards and other regulations. AS3772-2008 Kitchen Cooking Equipment; AS 2444 Selection and Location of Portable Fire Equipment; AS 1851 Maintenance of Fire Equipment; and other local regulations. All equipment is required to be maintained in accordance with Standards, as well as manufacturer’s instructions. |
All STEPS must be completed at each 6 monthly service, and steps required for Annual Service are marked (Annual). For further details on the following procedures, refer to the Amerex Manual and to AS3772-2008. |
SCHEMATIC OVERVIEW OF TYPICAL SYSTEM
|
SYSTEM COMPONENTS:
• System Agent Cylinder
• Manual Pull Station(s)
• Distribution Network Pipes & Nozzles
• Detection Line
• System Activation Cylinder
• Control System PRM or MRM
• Fire Extinguishers per AS 2444
• Fire Blanket(s) AS 3504
THERE ARE DIFFERENT procedures for Pneumatic Release Module(PRM) compared to the Mechanical Release Module(MRM)
The standard Service time for a System is approx. 2 Hours for an experienced Technician. |
SPECIAL TOOLS Required to complete the Service |
• 3/8 Socket Drive and Extension
• Amerex KP System Lockout Tool (PN 12738)
• Small Nitrogen Cylinder with regulator and adaptor to complete the actuation test, and pressurise PRM |
• Amerex KP Cocking Tool (PN 13341)
• Degreasing Solution
• Silicon Grease |
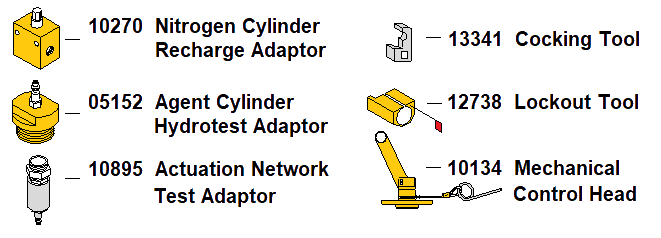 |
REVIEW KITCHEN AREA |
• Compare the current system/kitchen appliances to the original design. If changes, check compliance (Annual)
• Check fire system components are suitable for environmental conditions (Annual)
• Check detection coverage. Are there any unprotected hazard areas? (Annual)
• Check the condition of the hood and plenum for grease build up
• Check warning Signs as per AS3772 |
BEFFORE SERVICING ISOLATE FROM FIP |
• The System MUST be connected to FIP. Isolate from FIP. This will allow the technician to test the alarms while ensuring that no alarms are sent to the Fire Brigade. |
DISARM THE SYSTEM |
Install the lockout tool (P/N 12738).
This tool will stop collapsible column from moving and activating the system.
This LOCKOUT TOOL is required for both the MRM and the PRM |
Unscrew and remove nitrogen cylinder.
Check the pressure on the bottom of the cylinder and replace as necessary.
In PRM do not remove the Accumulator assembly |
MRM SYSTEMS only release tension on the detection cable by gently pulling the tension bar down.
This will remove tension from the detection cable and allow fusible links to be serviced if the tension is not released the fusible links will not be able to be properly serviced.
|
AGENT CYLINDER |
• Check the pressure of the cylinder as per the gauge
• Check that the brackets are intact, not damaged and are adequately holding the cylinder in place
• Check cylinder, hose, pipes and fittings are intact and not damaged
• Note date of manufacture on agent cylinder
PRESSURE TEST OF AGENT CYLINDER EVERY 10 YEARS
• Subject the cylinder to a hydrostatic pressure test every 10 years, and replace agent
• Service to be done by Authorised agent and must use ONLY genuine Amerex Parts and Recharge Agent. |
SYSTEM ACTIVATION – NITROGEN CYLINDER |
• Check Pressure
• Check Date of Manufacture (Annual)
• Replace Nit Cylinder every 10 years or after any Discharge |
DISTRIBUTION NETWORK (Including Pipework and Nozzles) |
• Remove nozzles, clean and replace noting nozzle number and position. Clean dirty nozzles using degreaser
• Check each nozzle type is appropriate for its appliance (see list for nozzle types)
• Ensure blow off caps are in place on each nozzle and replace any that are missing,
• Check pipes, fittings and supports are intact and not damaged
• Conduct a clear passage test using dry nitrogen, to ensure unobstructed flow and to check for any leaks
• Check piping has not been moved and is aimed accurately at its appliance |
MANUAL PULL STATIONS |
• Test each manual pull station to ensure correct activation of the system. Reset system after each test if multiple pull stations are installed. Testing of cable is not sufficient, MUST test at each pull station.
• Ensure correct activation of any equipment shutdowns
• If connected to a FIP, check that alarm registers and all relevant sirens activate. Check that safety ties/anti-tamper seals are intact and secure,
• Check pull pins are in place and secure,
• Check actuators are clean and accessible |
MRM INSTRUCTIONS – This uses spring loaded with mechanical detection cable as detection system with fusible links placed throughout. When the fusible links are exposed to fire they break, releasing tension on the cable system, which activates the system. |
• Check cable for grease build up and burn marks, and fraying of cable
• Check fusible links are intact and undamaged. Remove, Clean, inspect and Replace ALL fusible links. Any damaged links to be replaced.
• Ensure brackets, supports and fittings are intact and undamaged,
• Check tension on detection cable and re-tension as necessary.
• Check detection coverage. Are there any unprotected hazard areas?
• Cable should be replaced every 2 years in high use(24hr/day) kitchens
FIGURE A : Not enough cable tension. The lever and pawl must be pulled downward while the ratchet pulley is prevented from rotating. Approximately 2-4 more clicks are required from this position; then raise spring tension bar and re-examine results. Caution: The MRM may inadvertently cause system discharge if left in this position.
FIGURE B : Proper Cable Tension. is obtained when the bottom edge of the linkage bar is aligned within the gray “pie” region of the indicator label, with the spring tension bar in the “up” position. Stand directly in front of the MRM while viewing. The lower edge of the linkage bar will essentially be horizontal.
FIGURE C : Too Much Cable Tension. Lower spring tension bar and unhook the blue spring from the tension bar, releasing all tension. Caution: damage to the MRM can result from careless over-tensioning of the assembly. |
PRM INSTRUCTIONS – The detection system consists of tubing which is pressurised through an accumulator, the tube is routed throughout the hazard area, when exposed to fire the tubing ruptures, pressure drops and the system fires. |
• Check detection tubing for grease build up and burn marks,
• Check detection tubing for breaks and weaknesses that could lead to breaks,
• Ensure brackets and fittings are intact and undamaged,
• Check pressure of the actuation cylinder inside the module and re-pressurise as necessary,
• Remove the actuation piston in the PRM to replace the o-ring (17692). Lubricate the piston before placing back. This MUST be done according to the manual.
• Check detection coverage. Are there unprotected hazard areas?
• Replace tubing every three (3) years.
• Check date of Manufacture of Actuation Cylinder (Annual)
• Hydrostatic Test of Actuation Cylinder every 10yrs |
EQUIPMENT SHUTDOWN |
• Check wiring of any installed equipment shutdown mechanisms – check fittings are intact and undamaged
• Air Handling System shutdown (Hood and Airconditioning)
• Electric Appliances shutdown (important for Electrical Safety during discharge)
• Gas Valve shutdown device(s)
|
FIRE EXTINGUISHER & FIRE BLANKET INSPECTION |
• Appropriate units in place as per AS 2444 – Inspection required at 6 monthly intervals
• Placement of units and Signage as per AS 2444
• Check Manufacture date of Extinguishers for pressure test requirements.
• Every Kitchen required to have Fire Blanket AS3772-2.4 |
RESET MRM |
• Follow steps exactly to avoid accidental activation of the system.
• Ensure all components are correctly in place,
• Using the Amerex Cocking Tool in conjunction with a 3/8” drive socket wrench + extension, re-cock the Collapsible Column . This is done by simultaneously pushing in on the Lock Spring while turning the Cocking Tool counter clockwise. The mechanism should now appear as depicted. Take care to push in the lock spring to ensure the nitrogen cylinder is not pierced when it is put back in.
• Firmly tap the side of the MRM unit to ensure system is cocked correctly.
• Install the Nitrogen cylinder.
• Replace anti-tamper seals/safety ties, System is now operational
|
RESET PRM |
• Followed steps exactly to avoid accidental activation of the system.
• Ensure all components are correctly in place,
• Rotate the Spring Loaded Lever clockwise (“1” in Figure A), until its tip is latched under the Trip Plunger. Resume pressurization of the Accumulator Cylinder to 70 PSI at 70°F (480 kPa at 21ºC). Leak check the fittings at both ends of the tubing. Re-make tubing terminations, if necessary.
• Using the Amerex Cocking Tool in conjunction with a 3/8” drive socket wrench + extension, re-cock the Collapsible Column (Figure A). This is done by simultaneously pushing in on the Lock Spring while turning the Cocking Tool counter clockwise. The mechanism should now appear as depicted in Figure B.
• Install the nitrogen cylinder.
• Replace anti-tamper seals/safety ties, System is now operational
|
REARM THE SYSTEM-CONNECT to FIP |
• Install the Nitrogen cylinder.
• Re-Connect to FIP |
|
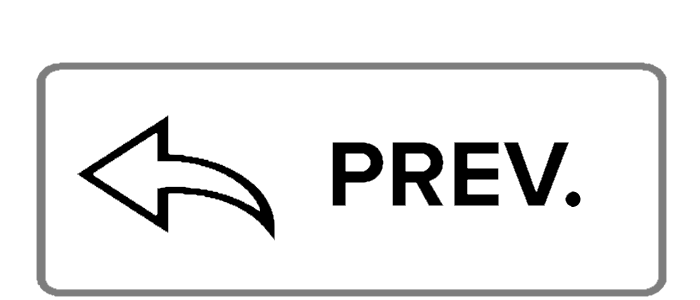 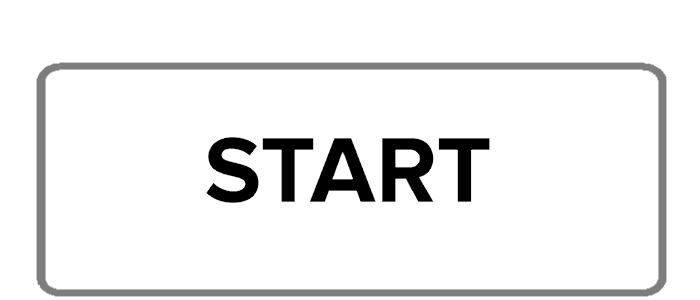 |